Pressure Equipment Inspection
Get in Touch
Other Services:
- Lifting Equipment Inspection
- Lifting Gears Inspection
- Scaffolding Inspection
- Marine Inspection
- Pressure Equipment Inspection
- Non Destructive Testing
- Torque Testing
- Anchor Bolt Pull Out Testing
- Tank Inspection
- Earth Moving Machinery
- Inspection Of Personal Protective Equipment
- Communication Tower
- Parks & Amusement Equipment
- Electrical System & Equipment Inspection
- Inspection Of Water System
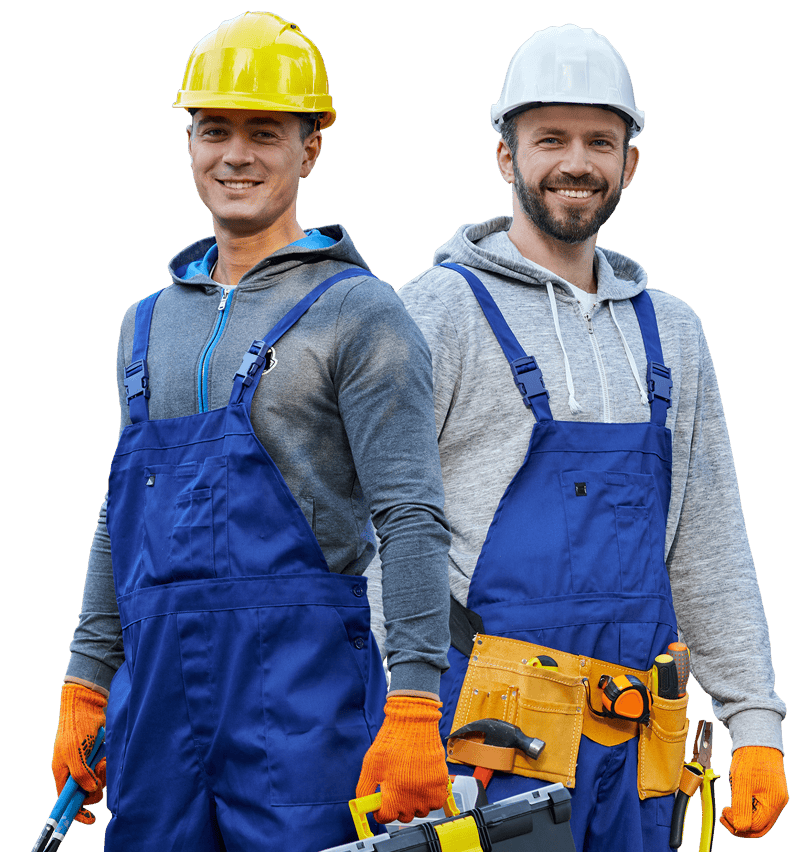
Pressure Equipment Inspection
Engineering managers and trained technicians are often responsible for inspecting industrial vessels designed to contain substances under pressure. Due to the safety risks associated with these vessels, standards bodies in most countries require regular inspections.
Inspections of pressure vessels can be either internal or external and vary from visual checks to specialized testing methods depending on the type of vessel. There are various types of pressure vessels, including fired and unfired vessels, each designed to safely contain specific substances at specified pressure levels.

Boilers Steam Boiler Inspection
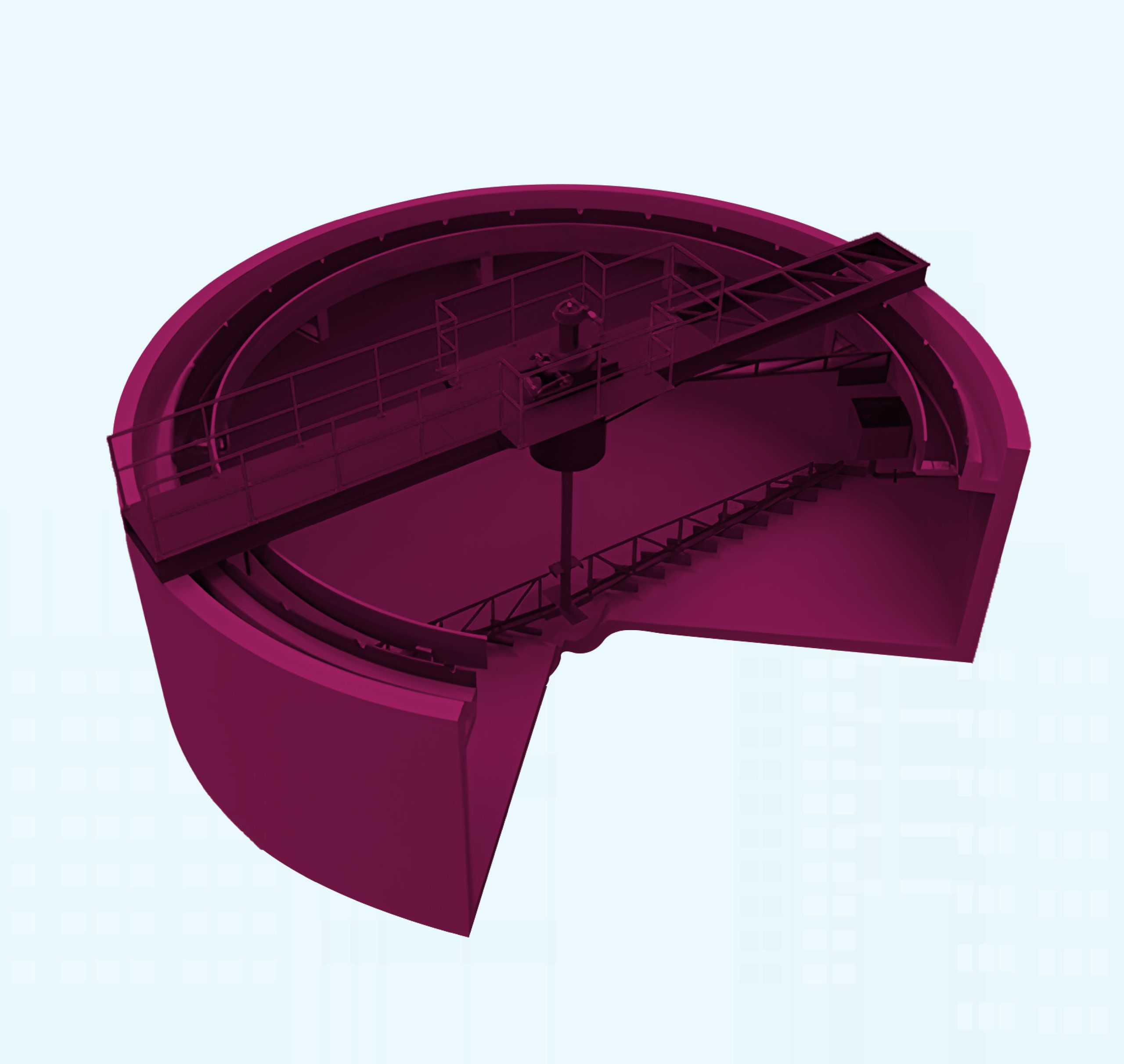
Clarifier
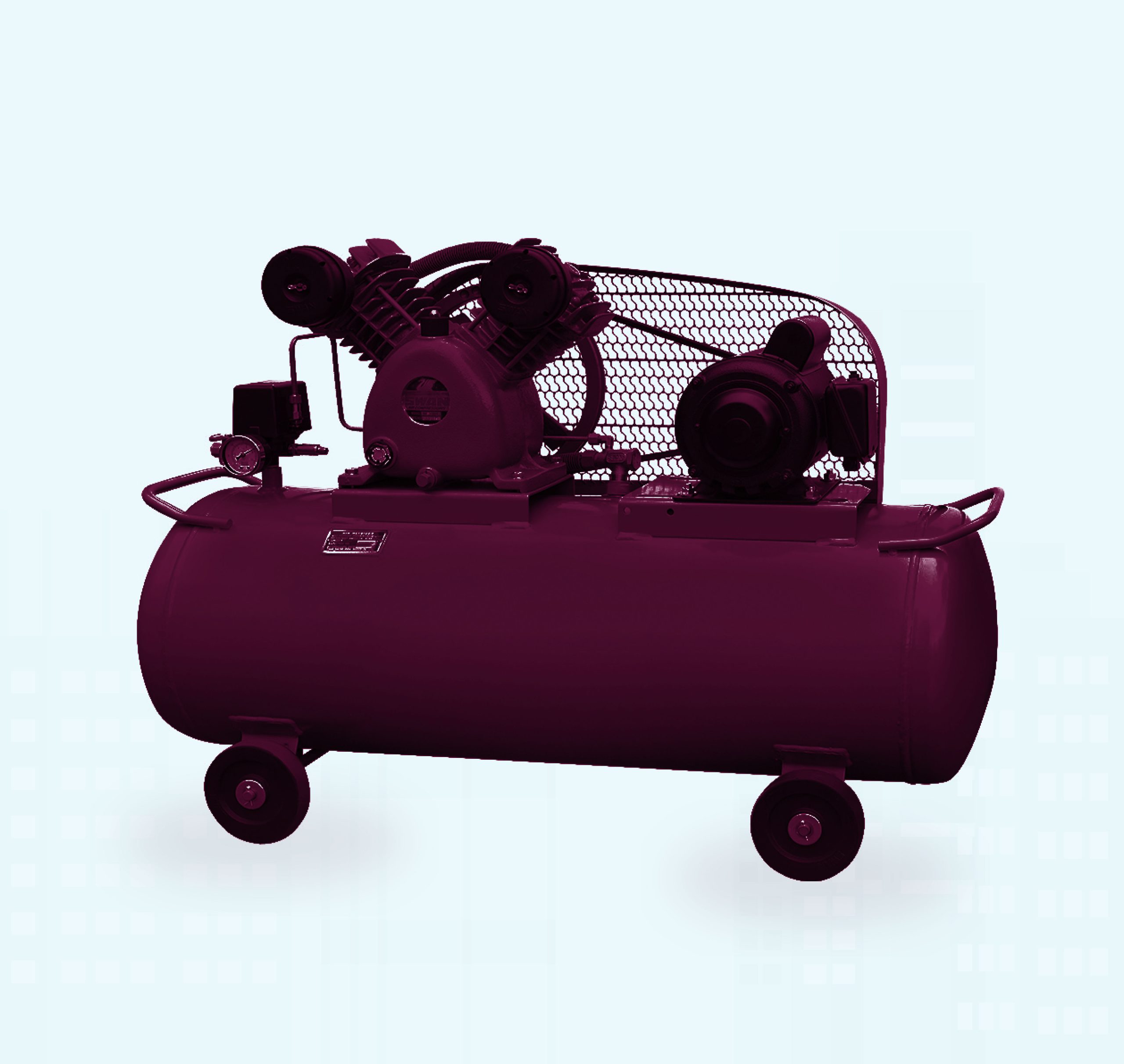
Air Compressor
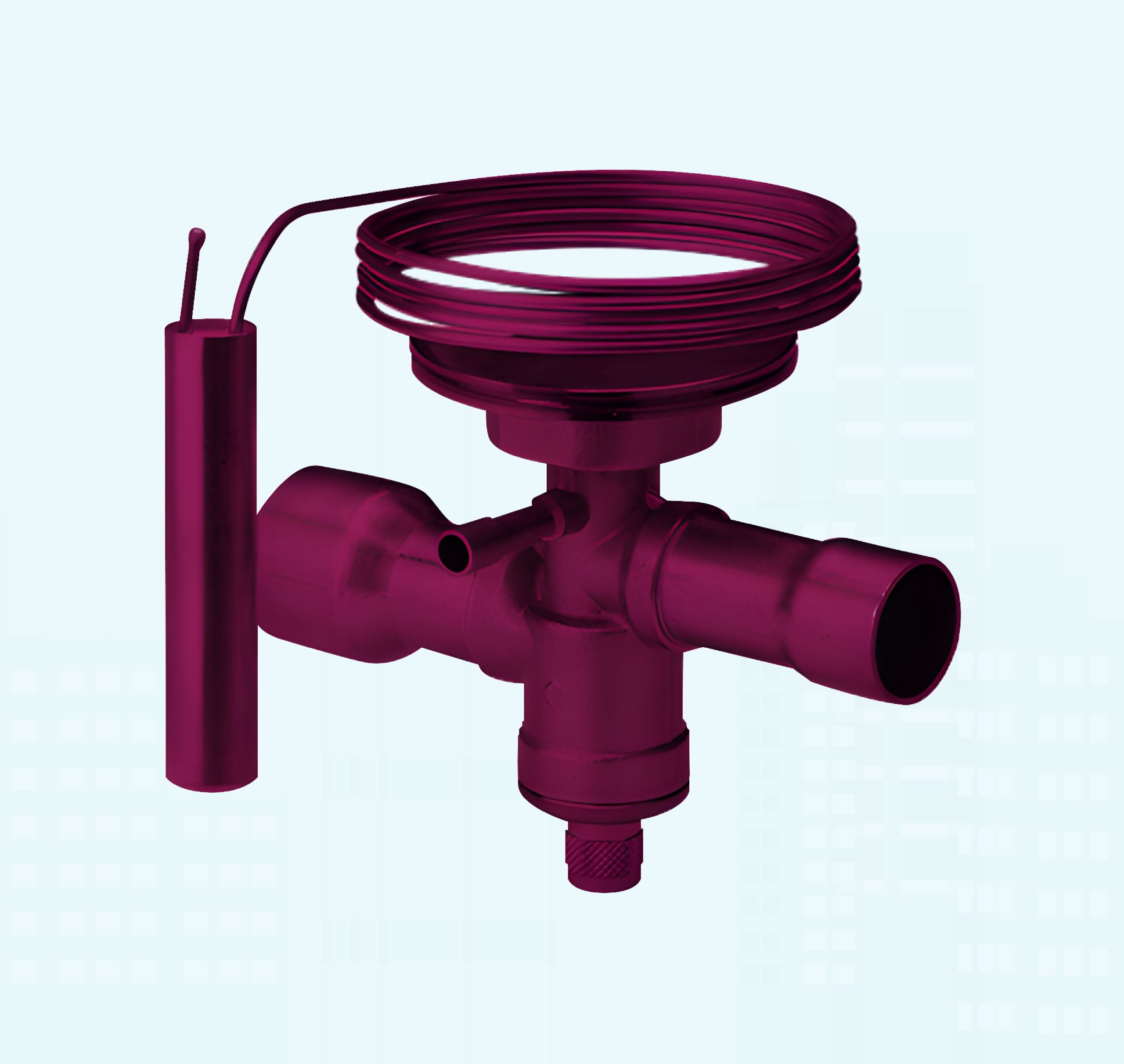
Expansion Valves
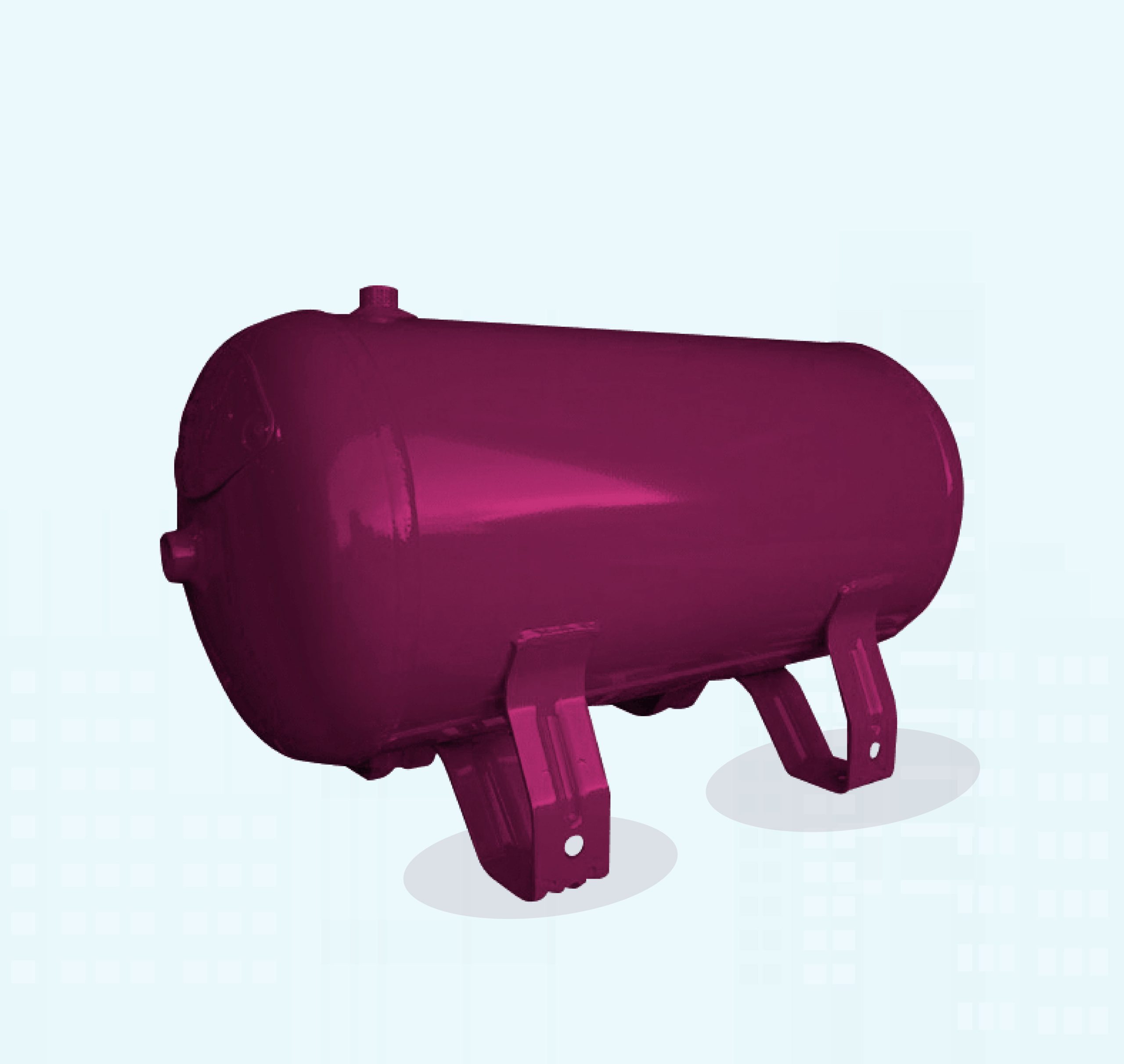
Air Receiver
The primary objective of an inspection is to ensure that the vessel material, connections, and components are in good working condition and comply with relevant safety standards or regulatory codes. Regular inspections are essential to ensure the safe operation of pressure vessels.
Importance of Pressure Equipment Inspection
Non-destructive testing techniques play a crucial role in certifying pressure equipment. These techniques evaluate the integrity of the manufacturing process and assess the mechanical quality of materials used in fabrication. They are essential for commissioning manufactured vessels and their component parts.
It is a challenging task, but evaluating potential mechanical defects is perhaps the most critical phase of the design process for pressure equipment. While much attention is paid to the geometry of the vessel to ensure uniform pressure distribution, the presence of invisible defects can compromise its integrity over time. These defects could have catastrophic effects once the vessel is installed and operating at its design pressure.
Every component, including welds, the crystalline substructure of the metal, and other parts, must function as a unified whole to withstand the stresses imposed by pressurized fluids and gases. Since the stored material often has explosive potential, a thorough pressure equipment inspection is essential to detect defects and prevent potential disasters. While mathematical calculations provide a degree of certainty, practical application requires a more rigorous assurance phase. This assurance is typically regulated by local authorities to ensure a safety margin is maintained.
The use of AICIP-accredited inspection routines and pressure equipment management strategies by a responsible engineering company is a significant allocation of company resources for pressure equipment inspection expertise. However, these routines and strategies only provide part of the picture when it comes to documenting a comprehensive life cycle evaluation.
The life cycle of pressure equipment is influenced by factors such as equipment geometry, material selection, welding techniques, and fabrication processes. However, other factors also play a crucial role. The final installation location is critical, considering whether the equipment will be above ground or installed below the surface. Environmental conditions, such as soil acidity, can significantly impact the equipment’s life cycle, especially when buried under erosive soil and moisture. In such cases, additional measures like cathodic protection assemblies may be required to protect the equipment and maintain its integrity.
Inspection techniques use technology to measure material thickness with ultrasonic instruments and examine the crystalline substructure of the alloy. Additionally, practical considerations from the installation site play a role in extending the equipment’s life. For example, adding rubber buffer plates as vibration absorbers can protect the equipment in seismically active regions, thereby extending its life
Pressure Equipment Inspection Solutions
Visual inspection is the most common non-destructive testing method for pressure vessels. During this type of inspection, engineering managers or trained technicians visually examine the interior and exterior of a vessel for signs of damage. They carefully assess the condition of vessel coverings, closures, insulation, joints, and structural connections.
Vessel inspections can be conducted manually by technicians or using unmanned aerial vehicle (UAV) technology. Drones make it easier and safer to inspect confined areas within pressure vessels or vessels located in hard-to-reach locations. Additionally, using drones can reduce inspection time, minimize the risk of injury to employees, and decrease equipment downtime.
Visual inspections may not always provide detailed enough data to assess the condition of a pressure vessel thoroughly. Surface testing can identify flaws on vessel surfaces, while volumetric methods detect internal flaws. Various testing methods are used to evaluate the integrity of pressure vessels:
- Dye penetrant: A liquid penetrant, sometimes containing a fluorescent chemical, is applied to a vessel's surface.
- Magnetic particle: A magnetic current is passed through a pressure vessel to detect flux leakage fields.
- Radiographic: Radiography is used to identify defects near or on the surface of a vessel.
- Ultrasonic: Sound waves are utilized to measure surface thickness, while volumetric testing detects flaws inside vessels.
Engineering managers can recommend the most suitable testing method for a pressure vessel and should consult relevant safety standards or regulatory requirements for guidance. Companies that develop digital checklists based on these requirements, along with any specific application measures, are more likely to comply with the best practices outlined in pressure vessel standards
WE ARE PASSIONATE
HONEST AND DEPENDABLE
WE ARE ALWAYS IMPROVING
Pressure Equipment Inspection Question:
Pressure equipment inspection is crucial for ensuring the safety of workers and the public, preventing accidents and complying with legal requirements.
The frequency of pressure equipment inspection depends on factors such as the type of equipment, its operating conditions, and regulatory requirements. In general, equipment should be inspected regularly to ensure its safe operation.
Pressure equipment inspections should be conducted by qualified and experienced inspectors who have the necessary knowledge and expertise in pressure equipment safety and regulations.
Failing to inspect pressure equipment can lead to accidents, injuries, and legal consequences. It can also result in equipment failure, downtime, and costly repairs or replacements